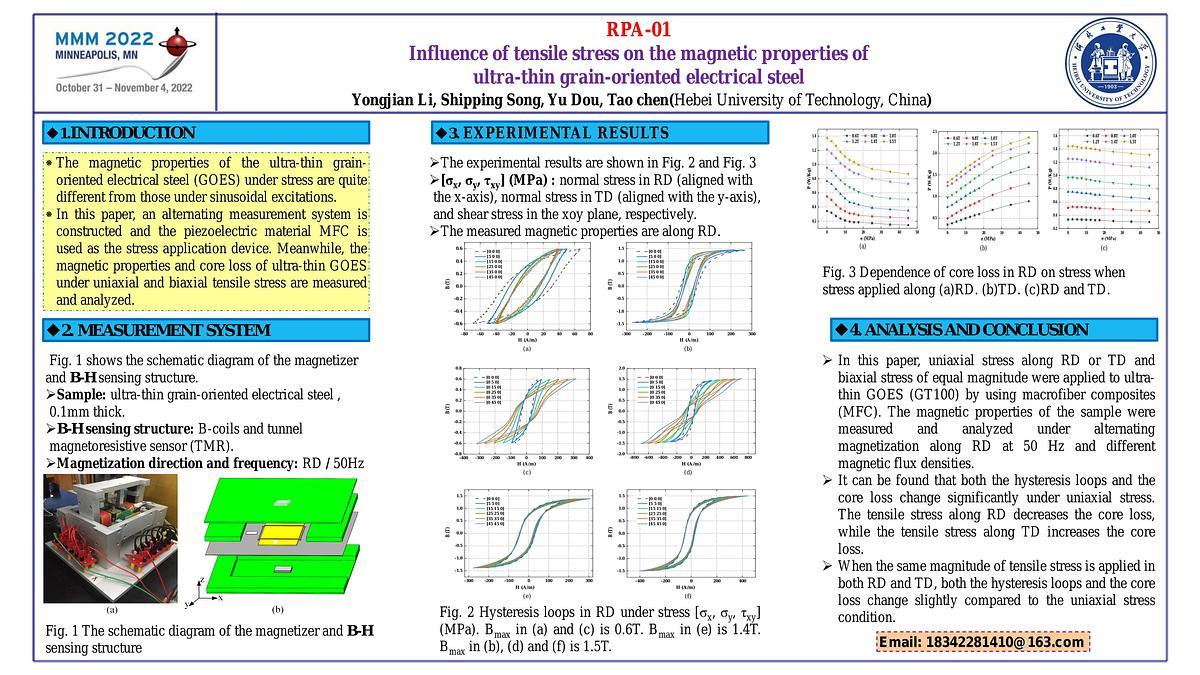
Premium content
Access to this content requires a subscription. You must be a premium user to view this content.
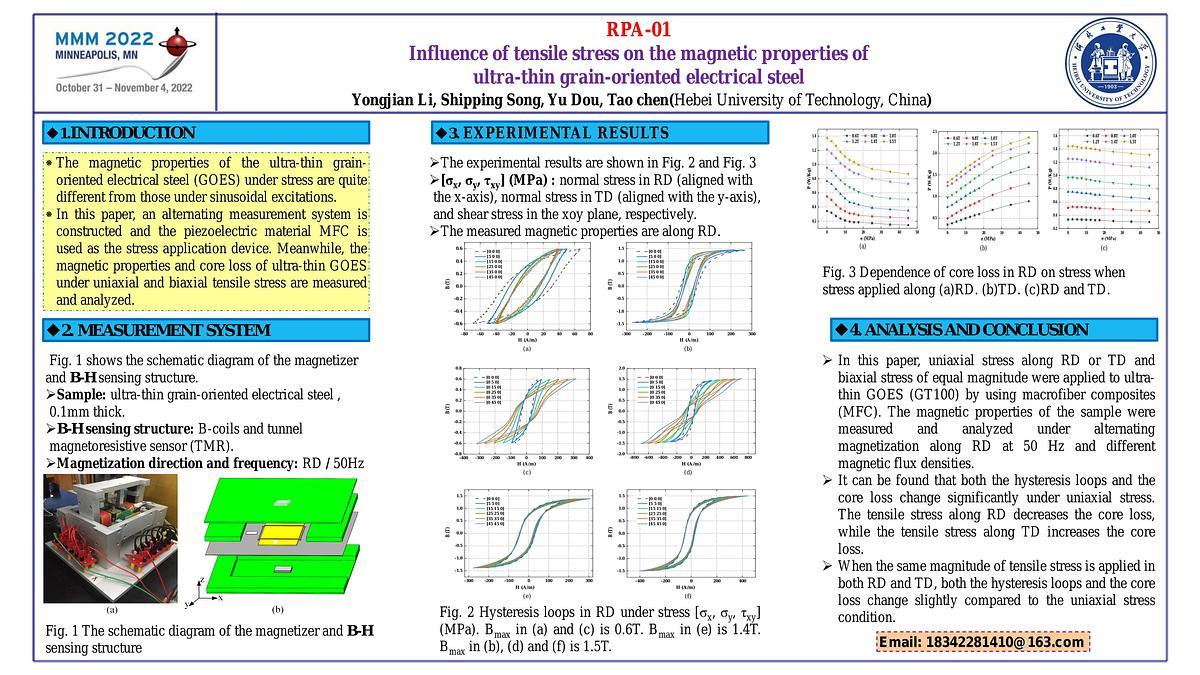
poster
Influence of stress on the magnetic properties of ultra thin silicon steel in high frequency range
Ultra-thin silicon steel with thickness less than 0.1 mm can be used to make the iron core of high-frequency transformers and high-speed motor. The design of these electrical equipment often relies on the data of alternating magnetic characteristics measured under standard excitation, ignoring the influence of working conditions such as stress and temperature, etc.. Under stress conditions, the magnetic properties of the magnetic material are quite different from those under standard sinusoidal excitation. Therefore, it is very important to accurately measure the magnetic properties of ultra-thin silicon steel under stress conditions.
Previously, many scholars have studied the influence of mechanical stress on the magnetic properties of conventional electrical steels 1-5. However, there are few reports on the properties of high frequency materials under stress. When testing the properties of high frequency materials under stress, we can refer to the traditional testing methods of silicon steel. Compared with the other methods of stress application, such as motor or oil pressure, piezoelectric material has good flexibility and control accuracy, and it will not produce stray magnetic field to interference the measurement. The most important thing is that piezoelectric materials have good applicability to the magnetizer. In other words, it is not necessary to reconstruct the magnetic circuit structure and stress actuator, and the relevant experiments can be carried out directly by pasting piezoelectric materials in the sample.
This paper uses the magnetizer proposed in paper 6, which has good test accuracy. The sample is ultra-thin silicon steel with 0.1 mm thickness (GT100). The size of the sample is 50 mm×50 mm. Two Macro Fiber Composite (MFC) 7 are symmetrically pasted on the upper and lower surfaces of the sample center. A maximum tensile or compressive stress of about 150 N or 107 MPa can be obtained in the sample along one direction. The distribution of stress is calculated by the FEM and shown in Fig. 1. It can be seen that the stress is uniform in the measuring region. Fig. 2 gives the hysteresis loops under different stress along rolling direction.
References:
1 Permiakov, V. , et al. "Loss separation and parameters for hysteresis modelling under compressive and tensile stresses." Journal of Magnetism & Magnetic Materials 272.supp-S(2004):E553-E554.
2 Singh, D. , et al. "Effect of stress on excess loss of electrical steel sheets." IEEE (2015):1-1.
3Hameyer, et al. "Effect of mechanical stress on different iron loss components up to high frequencies and magnetic flux densities." COMPEL: The international journal for computation and mathematics in electrical and electronic engineering 36.3(2017):580-592.
4Ali, K. , Atallah, K. and Howe, D. . "Prediction of mechanical stress effects on the iron loss in electrical machines." Journal of Applied Physics 81.8(1997).
5Naumoski, H. , Maucher , A. and Herr, U. . "Investigation of the influence of global stresses and strains on the magnetic properties of electrical steels with varying alloying content and grain size." Electric Drives Production Conference IEEE, 2015.
6Yue, S. , et al. "Comprehensive Investigation of Magnetic Properties for Fe–Si Steel Under Alternating and Rotational Magnetizations Up to Kilohertz Range." IEEE Transactions on Magnetics 55.7(2019):1-5.
7Wilkie, W. K. , et al. "Low-cost piezocomposite actuator for structural control applications." Proceedings of Spie the International Society for Optical Engineering (2000).