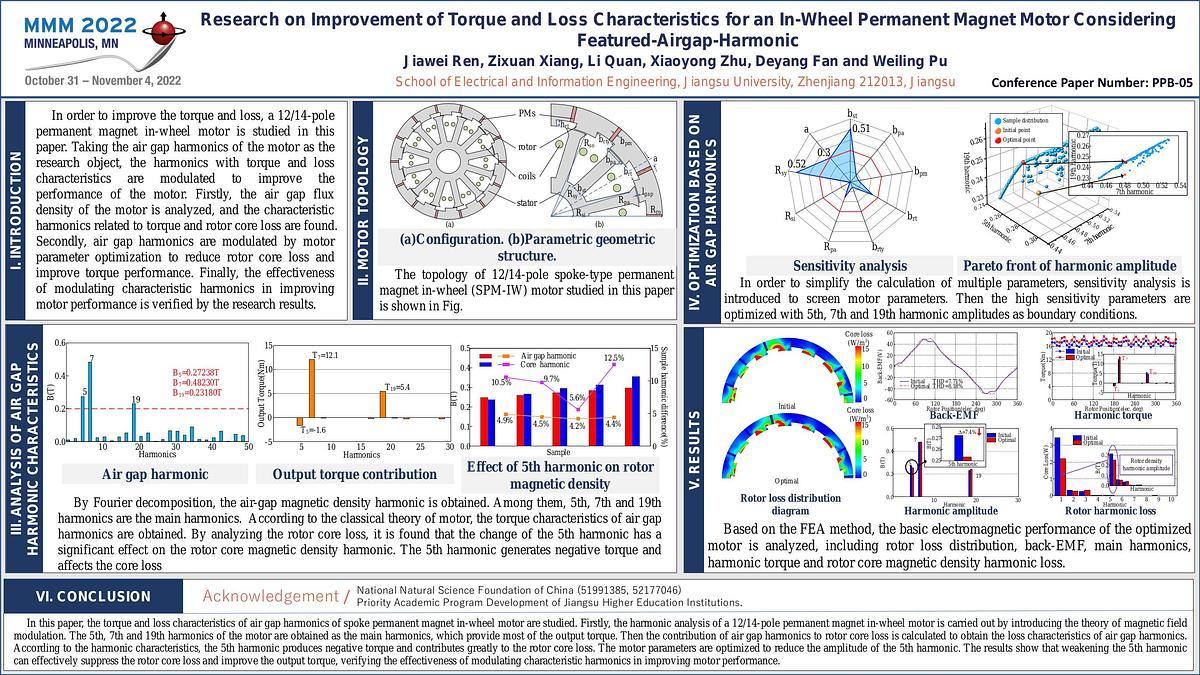
Premium content
Access to this content requires a subscription. You must be a premium user to view this content.
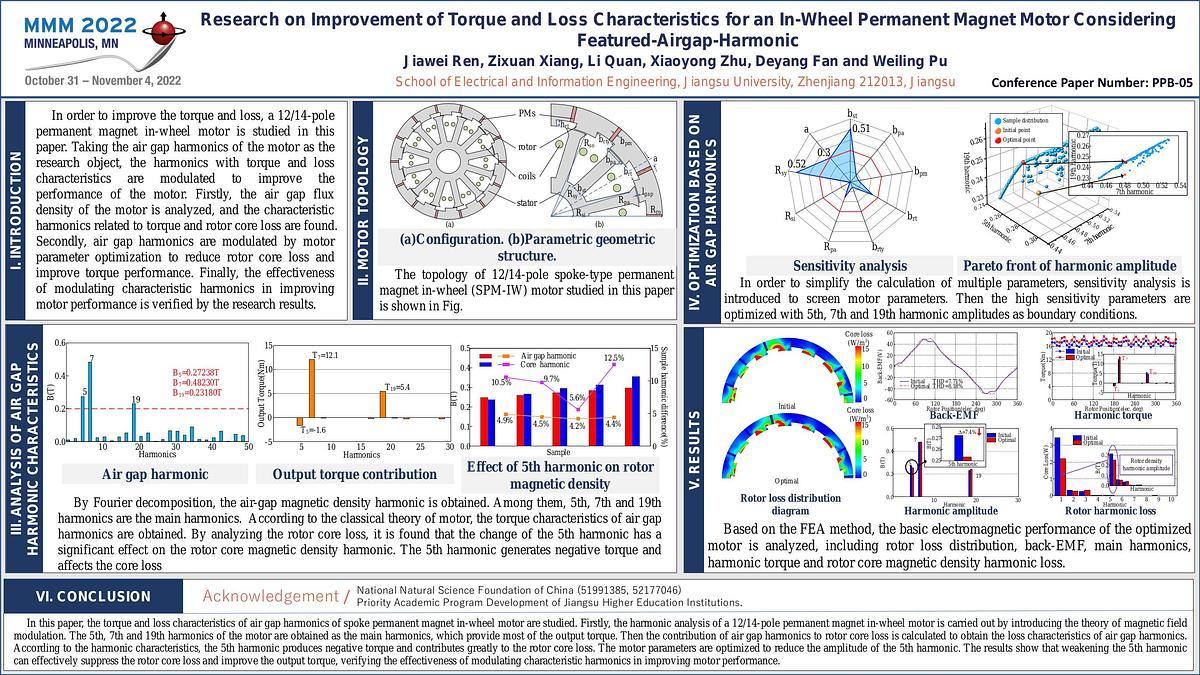
poster
Research on Improvement of Torque and Loss Characteristics for an In Wheel Permanent Magnet Motor Considering Featured
In-wheel motor technology is committed to provide a better travel for electric vehicles (EVs), which leads the way to innovation for a new generation of EVs. Quite
excitingly, the in-wheel motor generates power directly in vehicle wheel. It means that improved power performance and operation efficiency can be achieved potentially for the EVs with
in-wheel drive. Generally, the motor torque guarantees general drive requirements, while the loss determines operation efficiency. It is noted that, during the design process of motor, there
is relatively complex association between the two performances. Hence, how to obtain a capability of excellent low-speed large-torque and low loss characteristic is the essential entry point
for the study of in-wheel motor 1,2.
In this paper, the research on improvement of torque and loss characteristics is presented for a spoke-type in-wheel PM (SIW-PM) motor. In the perspective of flux modulation, a concept
of featured airgap harmonic is introduced into the motor design. By purposely designing the featured harmonic, a well tradeoff is realized between the torque and loss of SIW-PM motor.
Fig. 1 shows the topology of the motor. Fig. 2 shows an analysis of the amplitude of main harmonics, the torque contribution of harmonics, and the rotor magnetic density, in which the 5th
harmonic produces positive loss and negative torque. Reducing the amplitude of the fifth harmonic can effectively reduce rotor loss and improve the output torque. As is shown in Fig. 3,
sensitivity analysis is used to find the parameters with high sensitivity to 5th flux density harmonic amplitude 3. Fig. 4 shows Pareto front of harmonic amplitude generated by parameter
optimization, in which optimal sample is selected as optimization results. Fig. 5 shows the rotor core loss distribution before and after optimization. The comparison of torque and rotor loss
before and after optimization is given, as shown in Fig. 6 and Fig. 7. The results show that the rotor core loss is reduced and the output torque is increased by suppressing the amplitude of
the 5th harmonic.
More detailed analysis and experimental verification will be presented in the full paper.
References:
1 Z. Q. Zhu and J. T. Chen, IEEE Trans. Magn., vol. 46, no. 6, pp. 1447-1453, Jun. 2010.
2 X. Zhou, X. Zhu and W. Wu, IEEE Transactions on Industrial Electronics., vol. 68, no. 8, pp. 6516-6526, Aug. 2021.
3 G. Lei, C. Liu, and J. Zhu, IEEE Transactions on Energy Conversion., vol. 30, no. 4, pp. 1574-1584, Dec. 2015.