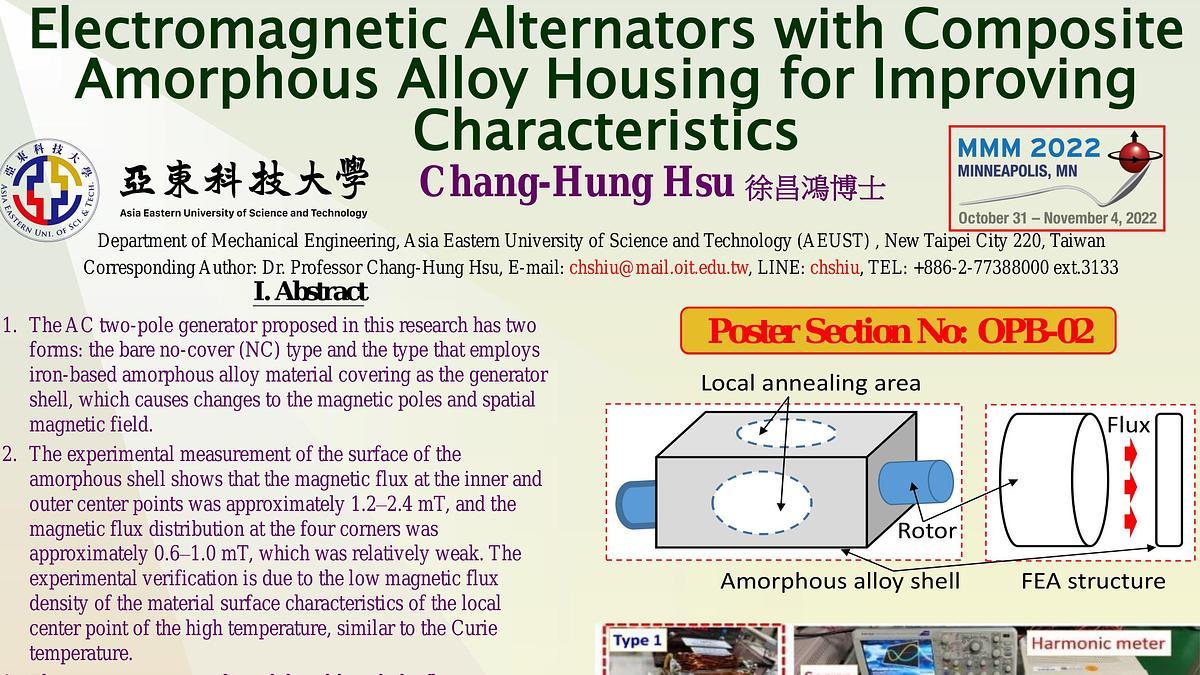
Premium content
Access to this content requires a subscription. You must be a premium user to view this content.
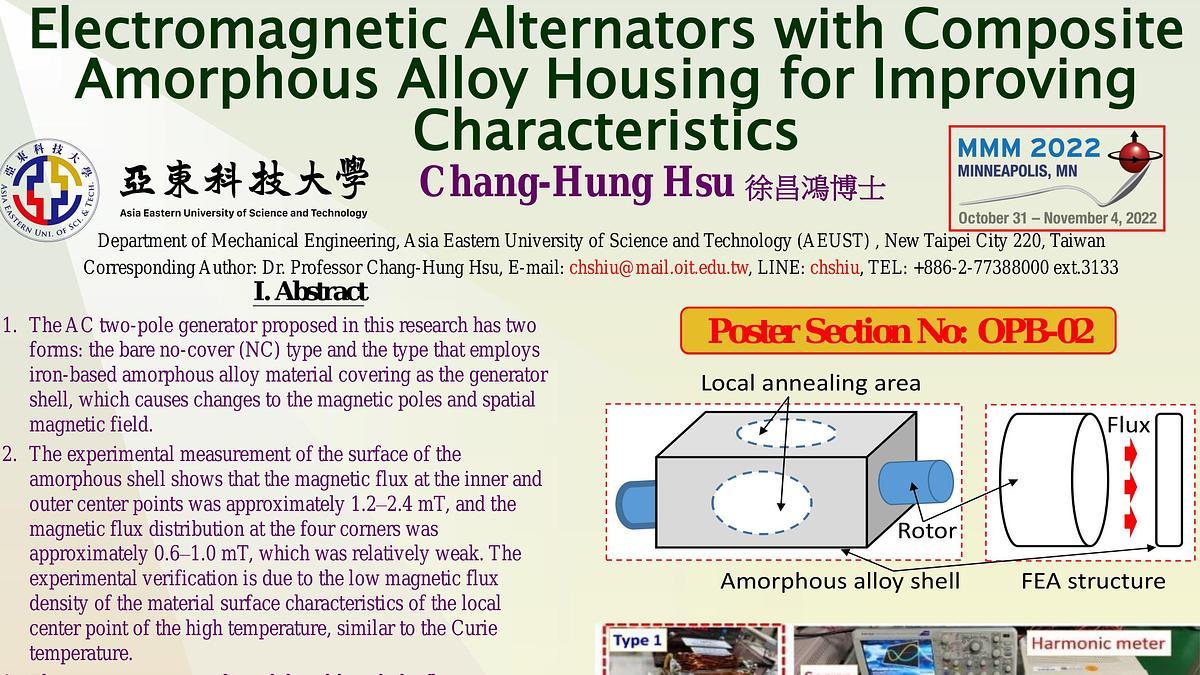
poster
Electromagnetic Alternators with Composite Amorphous Alloy Housing for Improving Characteristics
The AC two-pole generator proposed in this study has two forms, one is a non-cover (NC) naked motor, and the other is an iron-based amorphous alloy material as the outer casing of the generator (No Cover, NC). Cover with amorphous slice) for coating. Due to the change of magnetic pole and space magnetic field, different permanent magnet motors have magnetic material shell and no shell structure, as shown in Figure 1. Magnetic field distribution In the demagnetization area, the power and magnetic field changes are tested by order wave analysis and the surface magnetic flux density tester of amorphous materials. The order wave measurement results of different shell shapes can show the magnetic flux density node in the magnetized direction of the demagnetization area. cover. In the experimental measurement of the surface of the amorphous shell, the magnetic flux at the inner and outer center points is about 1.2-2.4 (mT), which is relatively strong, while the magnetic flux distribution at the four corners is about 0.6-1.0 (mT), which is relatively weak. The experimental goal is to set the effect of demagnetization on the electromagnetic parameters, and it is concluded that the permanent magnet salient pole motor has better generator power characteristics in the cladding demagnetization and the magnetic flux distribution of the amorphous shell. In addition, the experiment is also carried out and a local flame is proposed. The annealing process method is used as the coating of the generator and the measurement of the magnetic properties. The experimental verification is that the magnetic flux density of the material surface at the local center point of the high temperature is close to the Curie temperature. The above, but the order wave and power performance of the generator of the flame partial annealing process are poor, as shown in Figure 2.