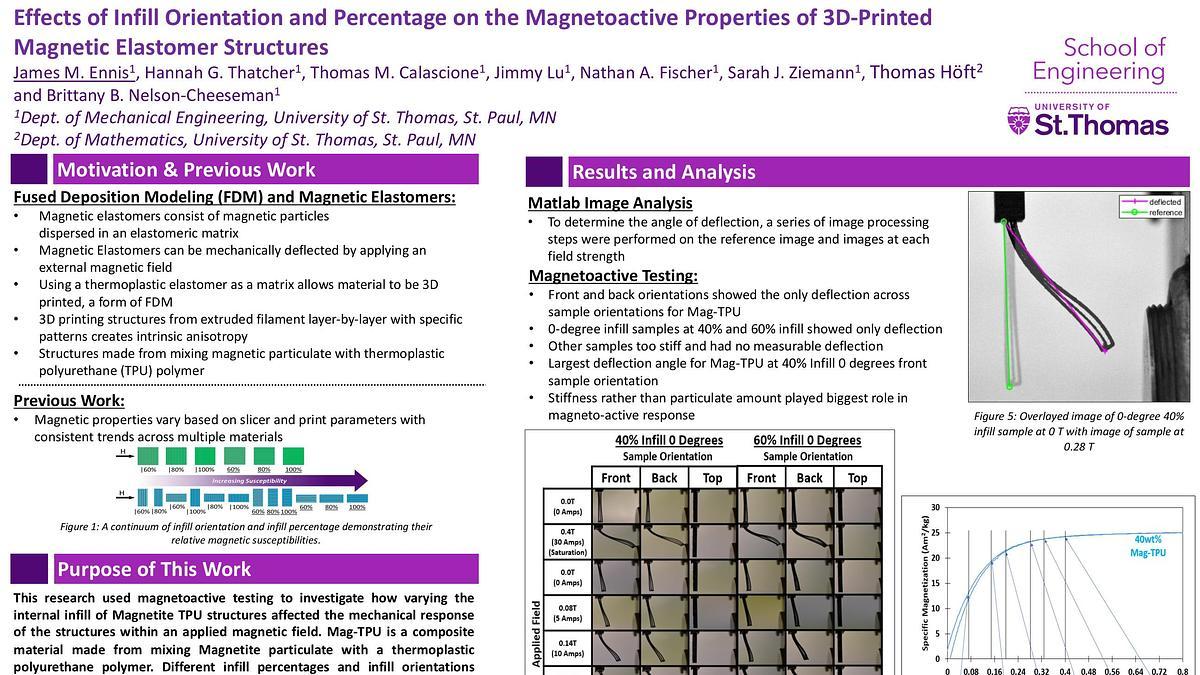
Premium content
Access to this content requires a subscription. You must be a premium user to view this content.
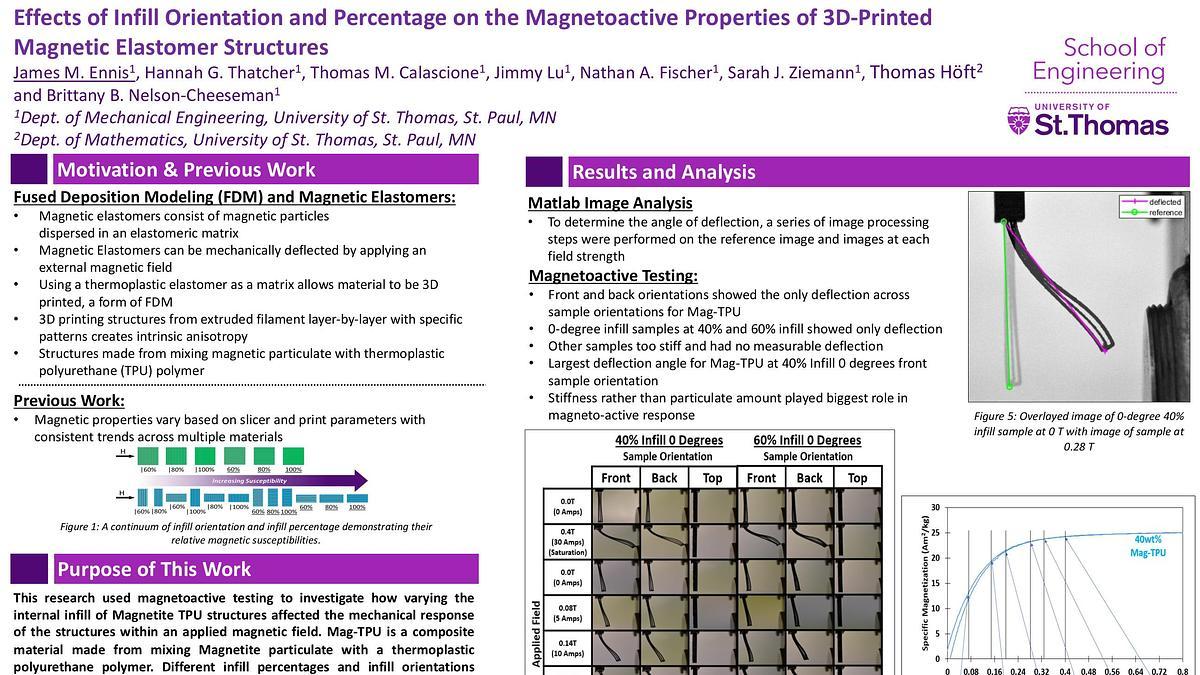
poster
Magnetoactive Properties of 3D Printed Magnetic Elastomer Structures: Effects of Infill Orientation and Infill Percentage
Magnetic elastomers are flexible smart materials that can be manipulated by magnetic fields to achieve reversible mechanical deformation. These highly configurable materials are instrumental in transforming biomedical applications such as artificial muscles, dampeners, and other vibration absorbers. Magnetic elastomer structures must be customizable to satisfy these complex applications leading to the use of fused filament fabrication (FFF) in creating them. FFF is a 3D printing process where material is extruded in 1D lines (infill) to build 2D planes layer-by-layer, resulting in a 3D structure. This research used magnetoactive testing to investigate how varying the internal infill structure affected the mechanical response of the structures within an applied magnetic field. Different infill percentages and infill orientations were tested to account for different mechanical stiffnesses and internal geometries. The elastomers were made by adding 40wt% magnetite (Fe3O4) to a thermoplastic polyurethane (TPU) matrix. Each sample was magnetoactively tested with three different transverse magnetic field orientations (Front, Back and Top). The samples were placed between two electromagnets, and the angle of deflection was recorded as a function of applied field. Maximum angles of deflection for the testing setup were reached when both lower infill percentages, translating to less material in the cross-section of the sample, and lower infill orientations, creating much less crosslinking between infill lines, were used. Transverse fields applied parallel to the print plane (Front, Back sample orientations) demonstrated the most magnetoaction due to less crosslinking constraining the bending stiffness. The anisotropy of the infill structure likely also contributed to the large response from certain samples. It was concluded that for this fixed base material, it is more important to 3D print structures with lower stiffnesses than more net magnetic particulate in achieving the most magnetoaction. According to this data, 3D printed magnetite-TPU structures are viable for creating components easily stimulated by a magnetic field unlocking many possibilities for the creation of useful technological components.