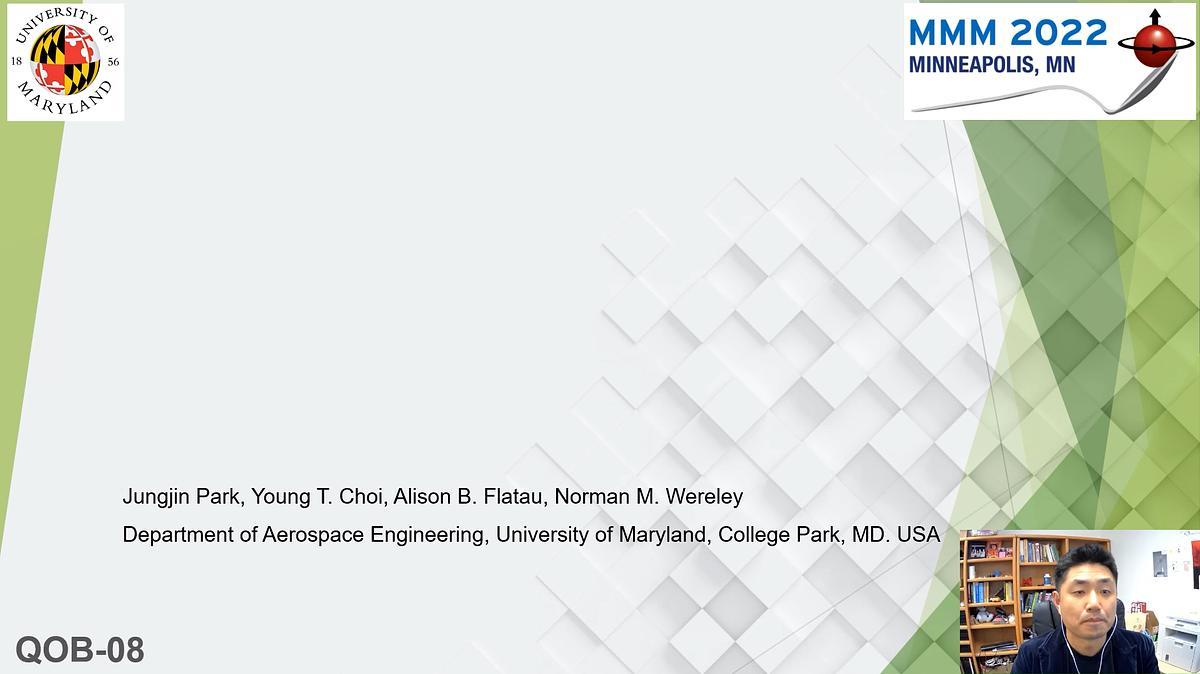
Premium content
Access to this content requires a subscription. You must be a premium user to view this content.
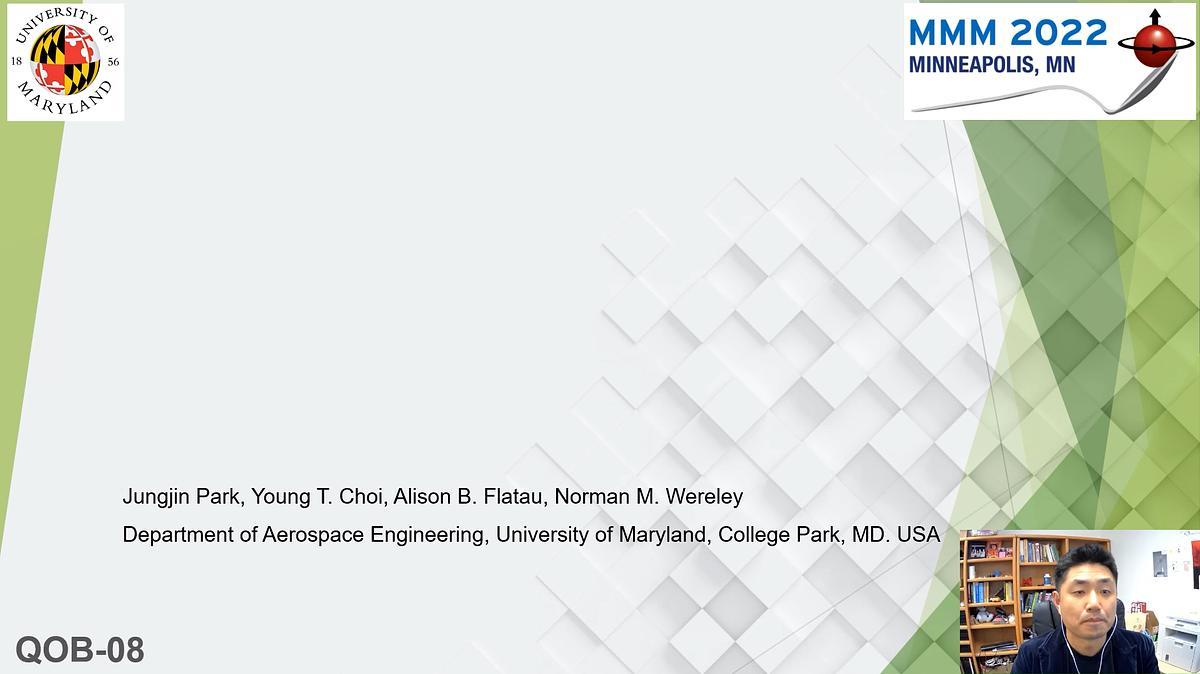
technical paper
Development of Magnetorheological Fluids within 3D Printed Elastomeric Cellular Structures with an Accumulator
Magnetorheological fluids (MRFs) consist of micron-sized magnetic particles dispersed in a carrier fluid for which rheological properties can be tuned reversibly with
magnetic field.1 If an MRF is contained in a cellular elastomeric encapsulant (CEE), its mechanical properties, such as stiffness and damping, can be controlled via magnetic field. Such
tunability can be exploited for adaptive vibration control or energy absorption systems. A magnetorheological damper often uses an accumulator to modulate pressure injected by external
forces applied to the damper.2 An accumulator is implemented into the cellular encapsulant to enable essentially incompressible fluid to enter the accumulator and to allow compression of
the cellular material to take place, and also enables a mechanical bulge stiffness to the design.
Here, MRF was prepared with silicon oil (40% vol. fraction). Thermoplastic polyurethane (TPU) was 3-D printed as the CEE system. (Fig. 1 a). The MRF was injected into the TPU-CEE,
followed by the printing of a sealing layer. The wall adjacent to the sealing layer had a circular opening and a TPU membrane was bonded to its perimeter so that the pressurized MRF
could flow through the opening and be accumulated in the resulting pocket.
An external magnetic field (0 and 7 kG) was applied along the sample longitudinal axis at the time of uniaxial dynamic testing with 5% pre-strain. The TPU-CEE samples were
characterized via force-displacement tests at 1 Hz under strain amplitudes. The MR effect on the dynamic stiffness is defined as the ratio of the dynamic stiffness under the maximum
magnetic field to the dynamic stiffness in the absence of a magnetic field. Dynamic stiffness in the presence as opposed to the absence of magnetic field was 264%. (Fig.2a) The area of the
force-displacement curve of the system with an accumulator is about 41% greater than one without an accumulator. The accumulator enhanced the increase in damping (Fig. 2b). The
increase in damping capacity generally increased as strain amplitude increased.
References:
- Ashtiani M, Hashemabadi SH, Ghaffari A. A review on the magnetorheological fluid preparation and stabilization. Journal of Magnetism and Magnetic Materials. 374, 716.
(2015)
- Yu, Jianqiang & Dong, Xiaomin & Wang, Xuhong & Pan, Chengwang & Zhou, Yaqin. Asymmetric Dynamic Model of Temperature-Dependent Magnetorheological Damper and
Application for Semi-active System. Frontiers in Materials. 6. 227. (2019)