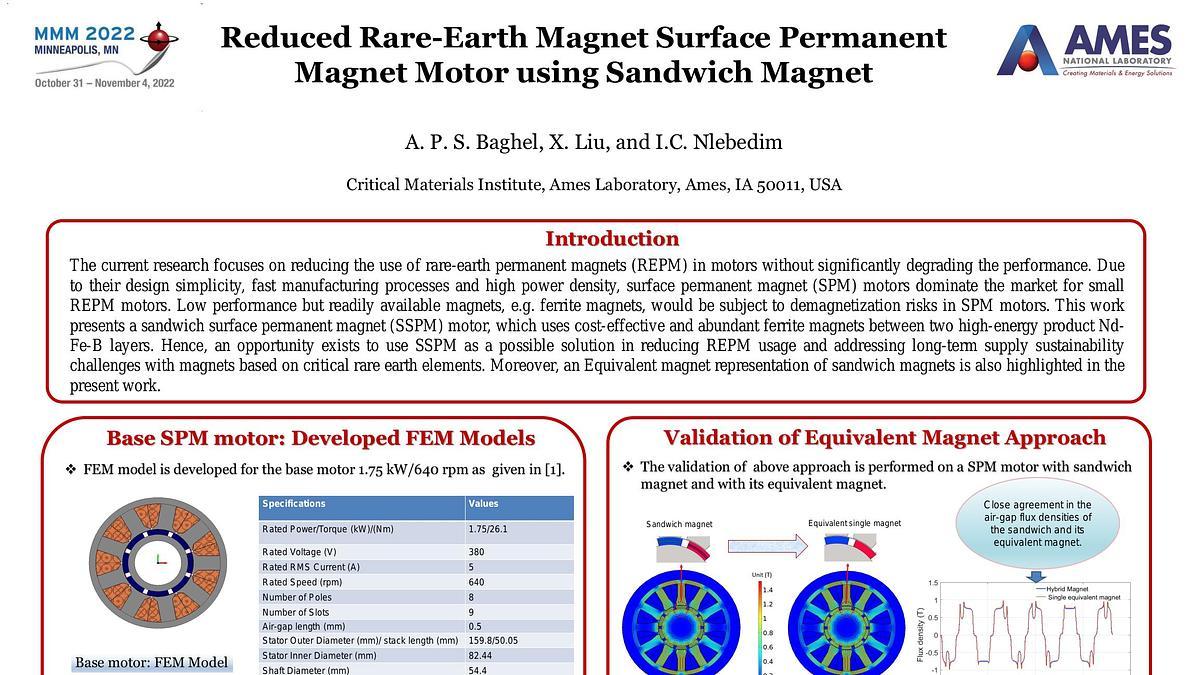
Premium content
Access to this content requires a subscription. You must be a premium user to view this content.
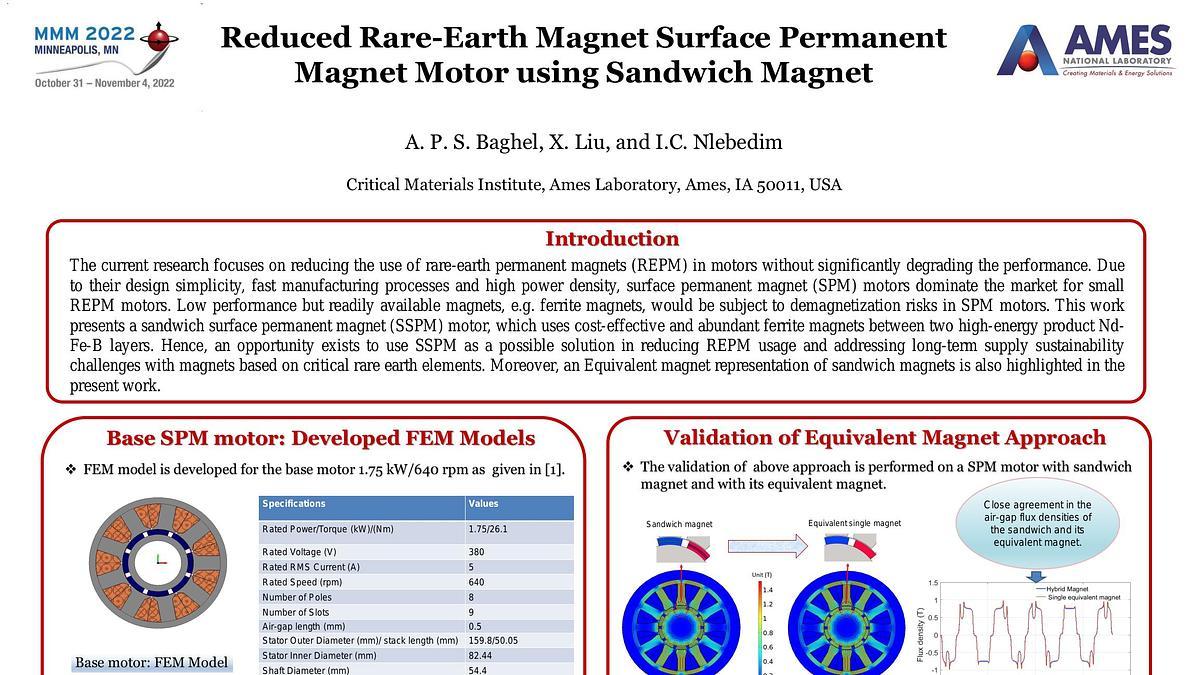
poster
Design and Analysis of Reduced Rare Earth Magnet Surface Permanent Magnet Motor using Sandwich Magnets
Surface Permanent magnet (SPM) motors are generally used in small traction applications due to high power density, simple designing and easy manufacturing processes.
SPM motors dominates the market particularly for small permanent magnet motors.However, the major concern with the SPM motors is their higher demagnetization risks due to close
exposure of PM to the stator windings 1. In order to avoid demagnetization risks, such motors use the critical rare-earth permanent magnets (REPMs) which are prone to supply disruption
and critical availability, hence poses a long-time sustainability challenge 2. Many attempts have been made 3-4, for reduction of critical REPMs in permanent magnet motors. However,
most of these attempts focus on the interior permanent magnet motors but rarely on SPM motors.
This work proposes a reduced rare-earth sandwich surface permanent magnet (SSPM) motor, which uses cost-effective and abundant ferrite permanent magnets (FPM, (BH)max=3 MGOe)
between two high-energy product rare-earth PM (Nd-Fe-B, (BH)max =33 MGOe) layers. The main idea of such a magnet structure is that the REPM drives the FPM to operate at higher
flux density which reduces demagnetization susceptibilities of the FPM without degrading torque capability of the motor. Equivalent magnetic circuit (EMC) approach is applied to
investigate the SSPM motor and the approach can also be applied to represent a sandwiched multiple type magnet structure with an equivalent single magnet. The performance of
sandwich-type magnets is carried out on a small traction motor (1.75 kW, 640 rpm motor) 5. The output torque and demagnetization performance of the motor with different magnets are
given in Table-I and Fig.1. The present work offers a way to reduce the consumption of critical REPM materials in PM motors without significant performance degradation.
This research was supported by the Critical Materials Institute, an Energy Innovation Hub funded by the U.S. Department of Energy, Office of Energy Efficiency and Renewable Energy,
Advanced Manufacturing Office.
References:
1 A. M. El-Refaie. T. M. Jahns, and D. W. Novotny, IEEE Trans. Magn., vol. 21, pp. 34-43, 2006.
2 R. T. Nguyen, D. D. Imholte, A. C. Matthews, and W. D. Swank, Waste Management, vol. 83, Pp. 209-217, 2019,
3 W. Wu, X. Zhu, L. Quan, Y. Du, Z. Xiang and X. Zhu, IEEE Transactions on Applied Superconductivity, vol. 28, pp. 1-6, 2018.
4 Y. Chen, T. Cai, X. Zhu, D. Fan and Q. Wang, IEEE Transactions on Applied Superconductivity, vol. 30, pp. 1-6, 2020.
5 N. Y. Braiwish, F. J. Anayi, A. A. Fahmy and E. E. Eldukhri, 49th International Universities Power Engineering Conference (UPEC-2014), pp. 1-5, 2014.