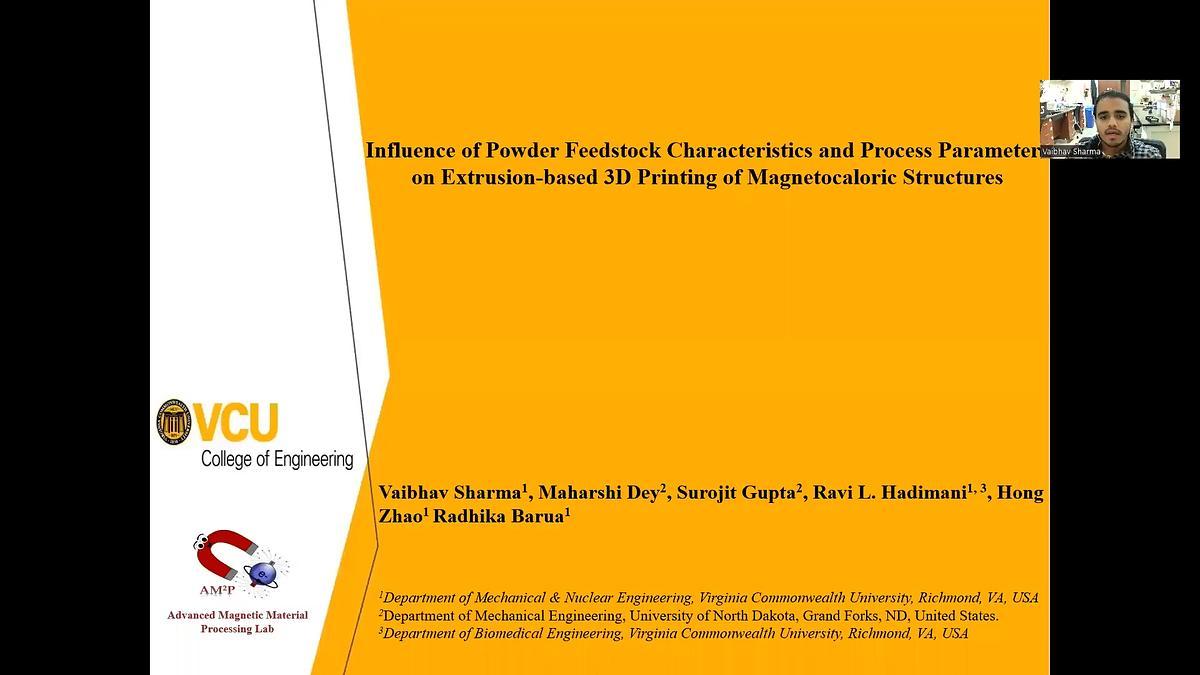
Premium content
Access to this content requires a subscription. You must be a premium user to view this content.
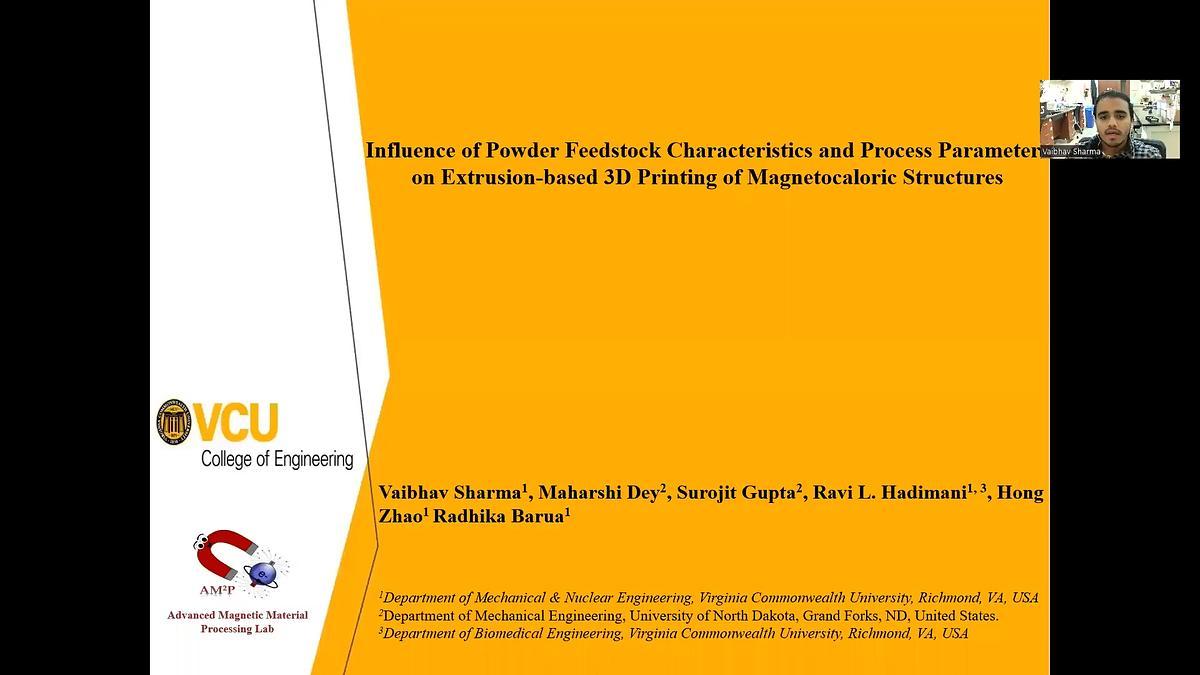
technical paper
Influence of Powder Feedstock Characteristics and Process Parameters on Extrusion based 3D Printing of Magnetocaloric Structures
Magnetic refrigeration is a sustainable, energy-efficient alternative to the conventional vapor-compression cooling technology. A key challenge in manufacturing magnetocaloric devices is that lack of fabrication methods for shaping the brittle caloric alloys into thin-walled channeled regenerator structures with optimized heat transfer properties, and gradient transformation temperature, while preserving the functional response of the materials system, Fig 1.1 To this end, we have recently developed a novel extrusion-based additive manufacturing (AM) method to 3D print spatially designed porous magnetocaloric structures with channel dimensions in the range 150-800 µm, Fig 2.1 Building on this proof-of-concept demonstration, research efforts pertaining to AM process development using three precursor magnetocaloric powders will be presented - (1) La0.6Ca0.4MnO3 nanoparticles (dia~10 nm) prepared by Pechiniuidelines for minimizing porosity and lack-of-fusion defects in the 3D printed magnetocaloric parts.