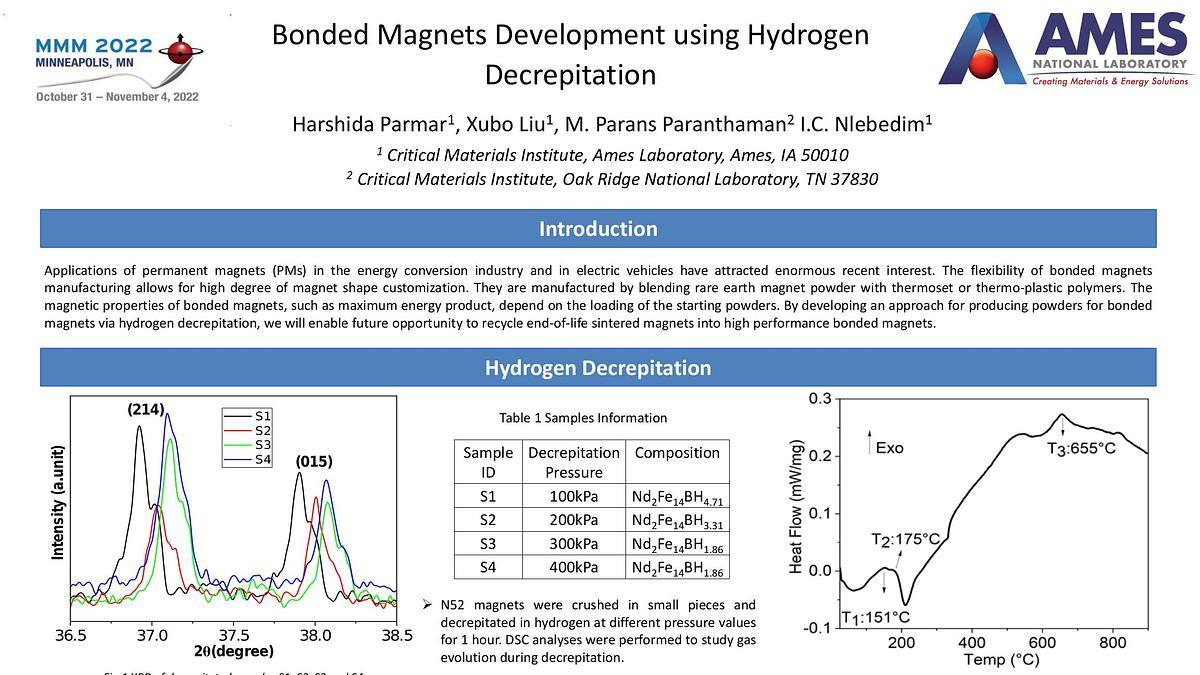
Premium content
Access to this content requires a subscription. You must be a premium user to view this content.
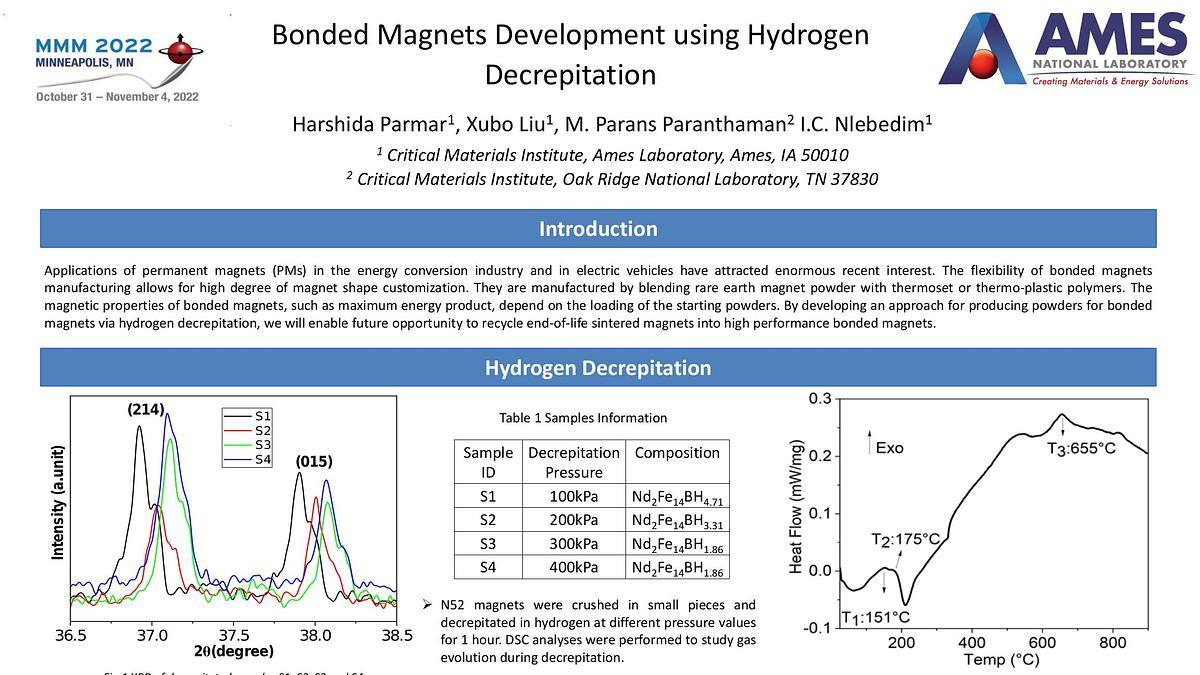
poster
Bonded Magnets Development using Hydrogen Decrepitation
We will present our results on the possibility of deriving high performance magnet powder for bonded magnets production via hydrogen decrepitation (HD) and heat treatment. Applications of permanent magnets (PMs) in the energy conversion industry and in electric vehicles have attracted enormous recent interest. The flexibility of bonded magnets manufacturing allows for high degree of magnet shape customization. They are manufactured by blending rare earth magnet powder with thermoset or thermo-plastic polymers. The magnetic properties of bonded magnets, such as maximum energy product, depend on the loading of the starting powders. By developing an approach for producing bonded magnets via HD, we will enable future opportunity to recycle end-of-life sintered magnets into high performance bonded magnets.
In this work, HD of N52 sintered magnets were performed at 1bar, 1.5bar, 2bar and 4bar pressure. The resultant powder due to the absorption of the hydrogen gas and pulverization of the material shows soft magnetic characteristics. The HD powder was characterized by DSC to find the degassing temperature. Fig.1 shows the DSC curve of 4 bar pressure produced HD powder. The peak at T1=151°C attribute to removal of H2 from Nd2Fe14B phase, T2=175°C conversion of Nd trihydride to Nd dihydride and the Peak at T3=655°C correspond to formation of Nd rich phase at grain boundary after degassing from NdH2 1. Hence, we carried out degassing in vacuum furnace at 800°C for 2h. The degassed samples show hard magnetic properties (Fig.2) however, final powder product magnetic property does not vary with pressure in HD process. Therefore, we selected the powder treated at 4bar, which shows 30 MGOe maximum energy product for bonded magnets development. The bonded magnets were developed by compression molding of a mixture of 60 vol% of magnetic powder and 30 vol% Nylon 12 at 180 °C for 5 min, followed by ambient cooling. Throughout the process, 3kPa pressure was applied to achieve maximum density. The bonded magnets had a density of 4.1 g/cc. Magnetic field alignment was performed on the bonded magnets at 180 °C under 0.8 T field to obtain 13MGOe maximum energy product.
References:
M.Zakotnik, E.Devlin, I.R.Harris, A.J.Williams, Journal of Alloys and Compounds,
450, 525-531, 2008
Fig. 1 DSC of HD powder
Fig. 2 MH loop of annealed powder