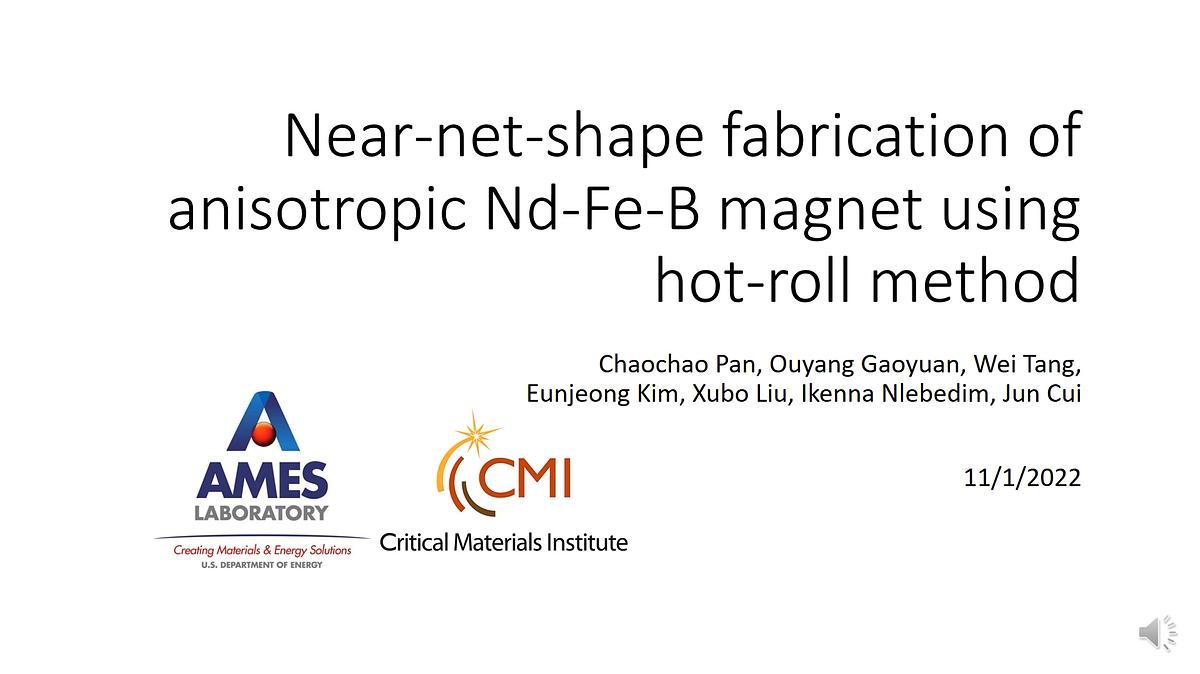
Premium content
Access to this content requires a subscription. You must be a premium user to view this content.
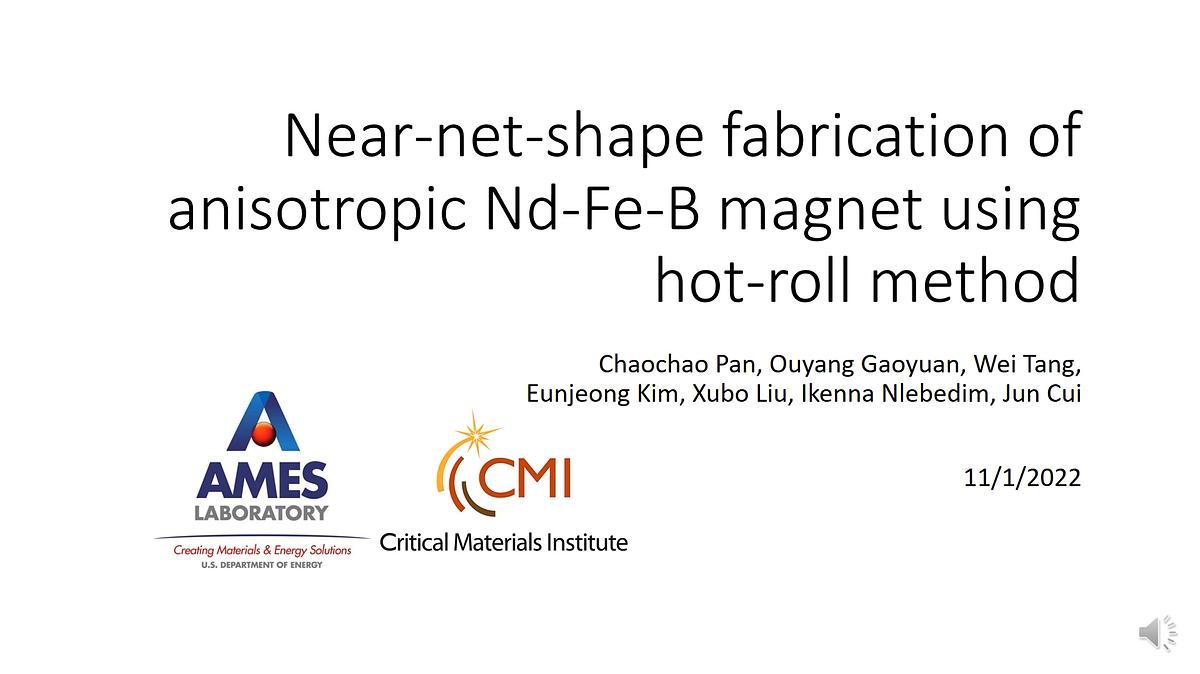
technical paper
Near net shape fabrication of anisotropic Nd Fe
Nd-Fe-B based magnet is the more powerful than any other magnets at room temperature. It plays a dominant role in energy efficiency and renewable energy applications due to its high energy density. However, making Nd-Fe-B magnets, especially into small sizes, can be challenging and costly. The part failure rate can be high during machining due to its brittleness. The reproducibility can be poor due to the variance in composition and microstructure inherent to the currently available fabrication methods. And the manufacturing cost is high due to the limited productivity of the batch based processes. Moreover, Nd-Fe-B needs heavy rare earth elements to be functional at higher temperature. These HRE are critical materials. One approach to bypass this HRE criticality issue is to utilize the grain size effect on coercivity, e.g., nanograin size magnet can perform the same as the micron-grain size magnet with 4-6% of Dy. However, making nanograin magnet requires a two-steps process: hot-press for densification and hot-deformation for texture. It is an inherently expensive process. Here, we report a novel Nd-Fe-B fabrication method that is continuous and near-net-shape. The process starts with loading Nd-Fe-B powders into a metal tube, packing the powder to 60% dense, then hot-rolling the powders into full density. We showed that hot rolling at 800°C with 70% thickness reduction can result in nearly full density (93%) anisotropic magnet with high energy product (31.6 MGOe). This novel method allows cost-effective production of near-net-shape Nd-Fe-B magnetic with good and consistent magnetic properties. Moreover, the method allows the making of continuous strip magnet that can be curved to match motor radius, making it possible to maximize the magnetic flux density on rotor circumference, thereby increase motor powder density.
References: