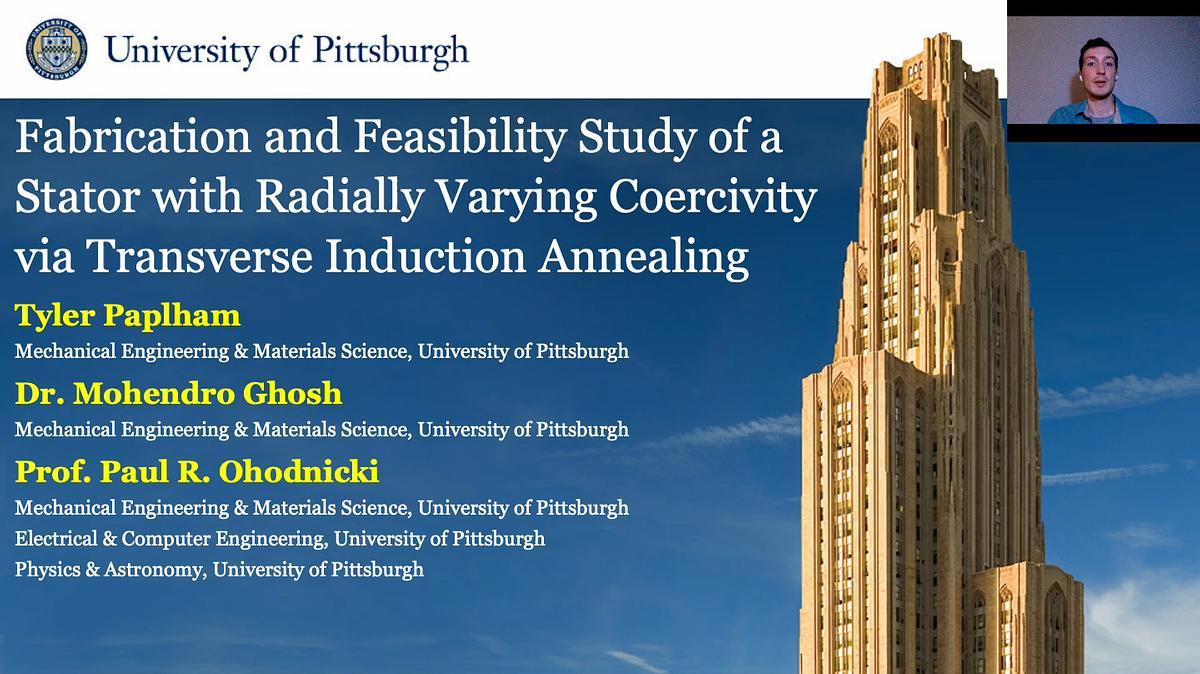
Premium content
Access to this content requires a subscription. You must be a premium user to view this content.
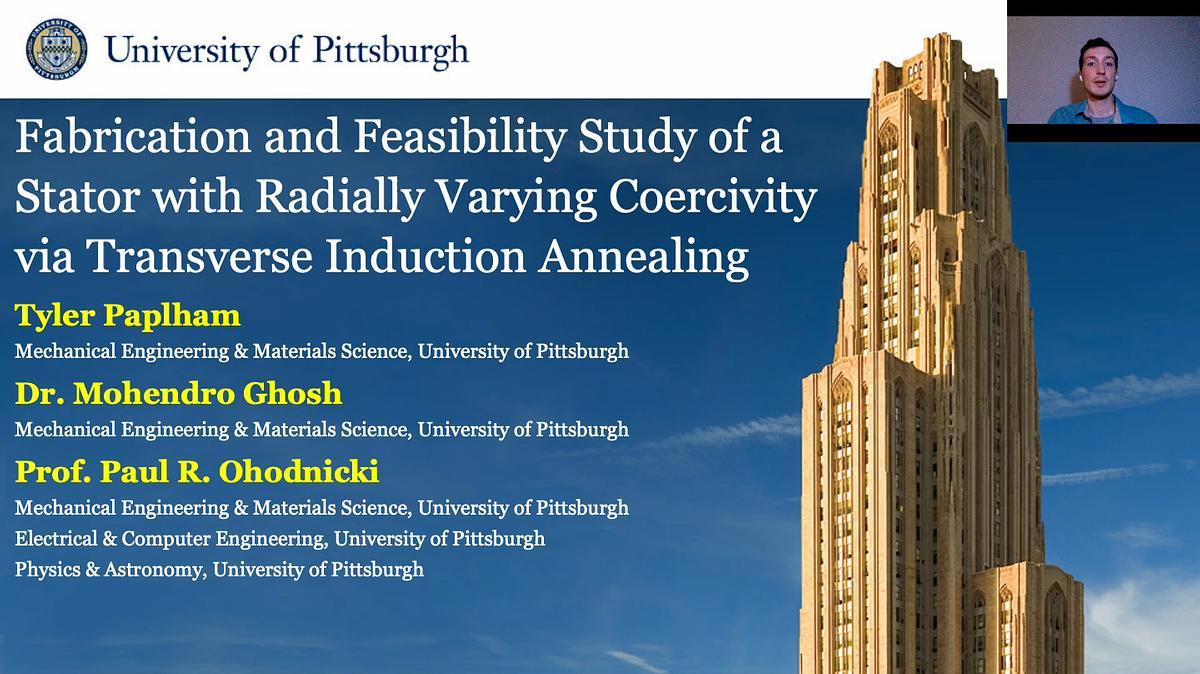
technical paper
Fabrication and Feasibility Study of Motor Laminations with Radially Varying Coercivity via Transverse Induction Annealing
The share of electric vehicles (EVs) on the road has seen a dramatic upward trend in the last decade as maximum range per charge has increased and the necessary infrastructure has grown to increase competitiveness with conventional gasoline-powered vehicles. However, maximal efficiency, achieved by minimizing the losses experienced by the motor stator and rotor, is limited by a tradeoff between low coercivity and high mechanical strength, which is necessary to withstand the significant torques experienced during operation 1–3. Radiofrequency (RF) transverse induction annealing (T-IA) is suggested as a novel pathway for imposing a continuous spatial variation in microstructure of bulk crystalline soft magnetic alloys 4,5. Via local control of grain size, magnetic and mechanical properties may be separately prioritized as functions of position, enabling fabrication of optimized motor laminations with reduced losses while still possessing requisite mechanical strength. Here we demonstrate through FEA modeling the dependence of achievable temperature profile on lamination and coil geometry, and we confirm feasibility of spatially optimized microstructure through experiments. We find that certain combinations of coil/lamination geometry may allow for simultaneous stamping of spatially optimized laminations, due to enhanced heating and higher temperature distributions in the region of the laminations where the magnetic flux density is greatest. We also present a basic feasibility modeling study examining performance of a motor containing motor laminations with radial variation in coercivity to motivate future work in this area.
References:
1 T. Sourmail, Prog. Mater. Sci., Vol 50, p.816–880 (2005)
2 P. Ramesh and N.C. Lenin, IEEE Trans. Magn., Vol. 55, 0900121 (2019)
3 T. Sourmail, Scr. Mater., Vol. 51, p.589–591 (2004)
4 A. Talaat, D.W. Greve, and S. Tan, Adv. Energy Mater., Vol. 2022, 2200208 (2022)
5 A. Talaat, D.W. Greve, and M. V. Suraj, J. Alloys Compd., Vol. 854, 156480 (2021)
Fig. 1: (a) Schematic of temperature/property profile achievable with a cylindrical coil as simulated in COMSOL Multiphysics (b) Experimental temperature profile observed with a cylindrical coil and square Hiperco lamination.