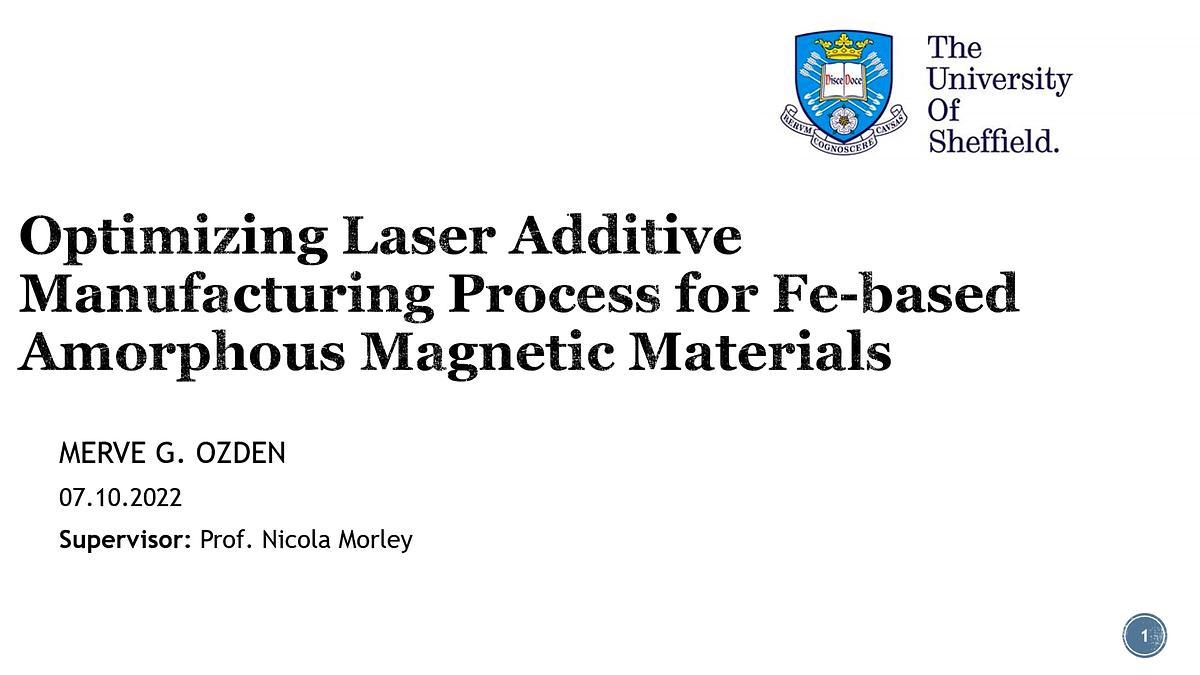
Premium content
Access to this content requires a subscription. You must be a premium user to view this content.
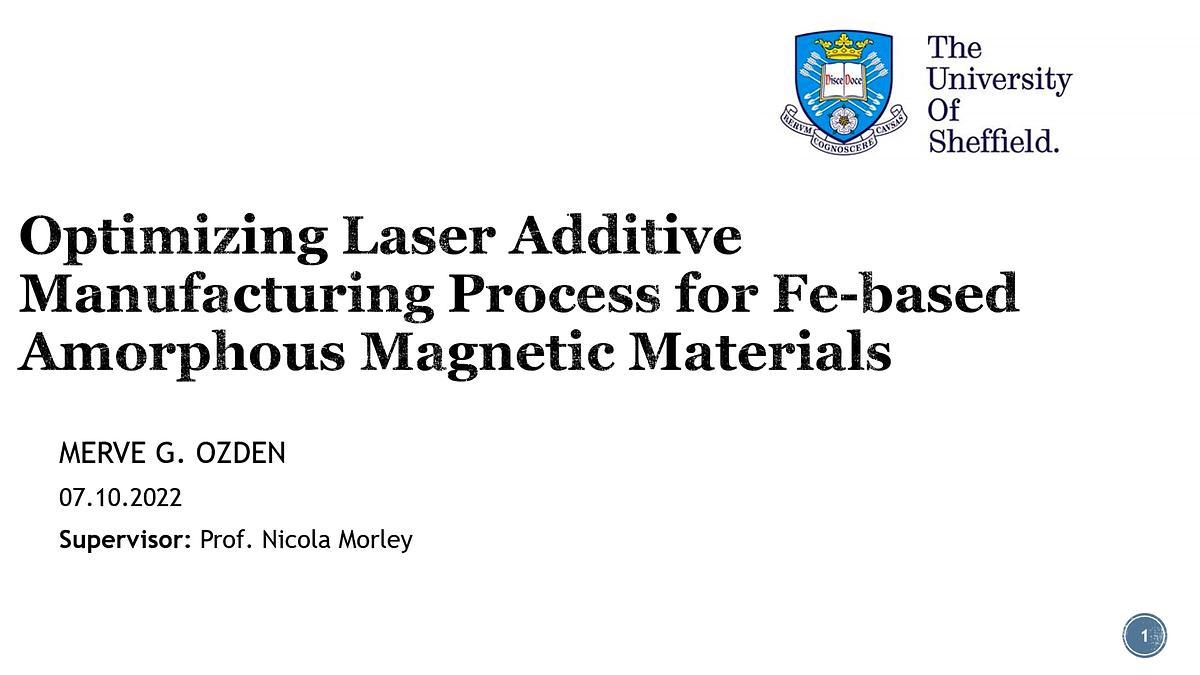
technical paper
Optimizing Laser Additive Manufacturing for Fe based Amorphous Magnetostrictive Materials
The process parameters optimization in laser powder bed fusion (LPBF) technique have been studied extensively by using the volumetric energy input (E=P/(v.t.h)) equation, which includes the major build parameters; laser power (P), scan speed (v), layer thickness (t) and hatch spacing (h) 1-3. Even though utilizing laser energy density to predict final properties of a specified materials is a good way to start, only considering this is not enough 4. Researchers have generally focused on the effect of laser power and scan speed on the final properties 5-8. This study indicates how major process parameters influence the physical and magnetic properties of LPBF-processed Fe-based amorphous/nanocrystalline composites ((Fe87.38Si6.85B2.54Cr2.46C0.77 (mass%)). The figure illustrates the magnetization (M)-magnetic field (H) loops corresponding sample microstructures fabricated by using same E (=60 J/mm3) and v (=1000 mm/s) and varying P, h and t (left corner). It is obvious that despite being printed with same energy density, changing h and t (Sample 1 and 2) or changing P and h (Sample 2, 3 and 4) led to the quite different results. It was found that bulk density improves as P increases, v, t and h decreases, i.e., high E is necessary, however, greater than 80 J/mm3 (due to the keyhole effect) and less than 45 J/mm3 (because of the insufficient energy input to the powder bed) causes either failing parts or large and high number of pores. Owing to the laser scanning nature, the microstructure evolves as molten pool (MP) and heat affected zones (HAZ) due to the high thermal gradient occurred between laser tracks 9. MP form around the scans, having Fe2B nanograins mainly, whereas HAZ generally contains α-Fe(Si) and Fe3Si nanocrystalline clusters. The sizes and quantities of those nanocrystallites determine the magnetic properties. With same E (60 J/mm3), v (1000 mm/s) and t (50 µm), only changing P and h caused samples to have different saturation magnetization; 206 emu/gr (P: 90 W and h: 30 µm) and 150 emu/gr (P: 150 W and h: 50 µm) (Figure).
References:
1 H. Gong, K. Rafi and H. Gu, Materials and Design, Vol. 86, p. 545-554 (2015).
2 S. Liu, H. Li and C. Qin, Materials and Design, Vol. 191, ID: 108642 (2020).
3 H. Gong, K. Rafi and H. Gu, Additive Manufacturing, Vol. 1, p. 87-98 (2014).
4 K. Prashanth, S. Scudino and T. Maity, Materials Research Letters, Vol. 5, p. 386-390 (2017).
5 S. Alleg, R. Drablia and N. Fenineche, Journal of Superconductivity and Novel Magnetism, Vol. 31, p. 3565-3577 (2018).
6 H. Jung, S. Choi and K. Prashanth, Materials and Design, Vol. 86, p. 703-708 (2015).
7 Y. Nam, B. Koo and M. Chang, Materials Letters, Vol. 261, ID: 127068 (2020).
8 D. Ouyang, W. Xing and N. Li, Additive Manufacturing, Vol. 23, p. 246-252 (2018).
9 C. Zhang, D. Ouyang and S. Pauly, Material Science and Engineering R, Vol. 145, ID: 100625 (2021).
Figure: M-H loops and micrographs of the samples LPBF-processed with same E (=60 J/mm3) and v (=1000 mm/s).